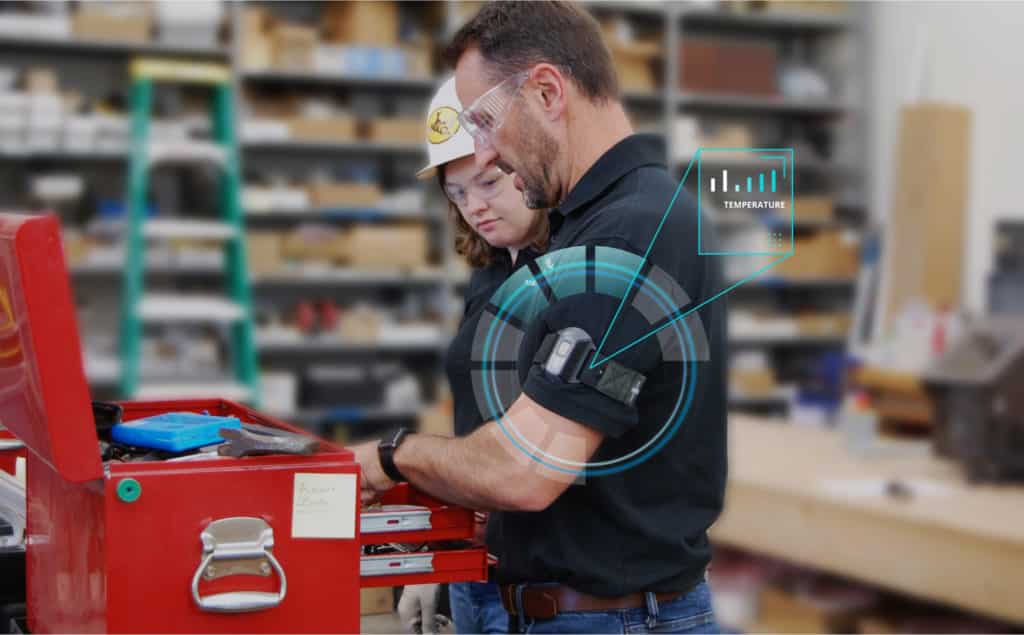
MakuSafe‘s IoT wearable technology, developed in partnership with PwC’s Surfaceink, is transforming industrial workplace safety through real-time environmental monitoring and data analytics, resulting in a 50% decrease in insurance claims among its industrial clients, according to a recent PwC case study.
The genesis of MakuSafe came from a simple yet profound conversation. Gabe Glynn, the company’s CEO and co-founder, was speaking with his father, a former factory safety manager, when a compelling question emerged: What if factories could monitor safety conditions even when safety professionals weren’t physically present on the floor? This conversation sparked a vision for a system that could provide near real-time environmental data to help improve efficiency while protecting workers.
The challenge was clear—factory safety professionals cannot be everywhere at once, yet hazardous conditions can develop at any time, according to PwC. The traditional approach to workplace safety relied heavily on periodic inspections and reactive measures after incidents occurred. MakuSafe’s founders recognized this fundamental gap in industrial safety monitoring and set out to bridge it with technology.
Development of Initial Prototype
Armed with this vision, the team began building a wearable prototype device designed to monitor various risk factors in industrial environments. The initial device incorporated sensors to detect high-decibel sounds, unsafe temperature and humidity levels, and low lighting conditions—all common environmental hazards in manufacturing settings, PwC noted.
A key feature of the early prototype was its accelerometer, which could identify when and where a worker experienced a slip or fall event. This capability addressed one of the most common causes of workplace injuries in industrial settings.
The founders quickly realized they faced challenges beyond the hardware itself. They needed solutions for managing the substantial data outputs, determining optimal placement of devices within factory settings, and perhaps most importantly, gaining worker acceptance of wearable monitoring technology, according to PwC.
Partnership with PwC’s Surfaceink
With a rudimentary functional prototype in hand, MakuSafe’s founders recognized they needed specialized expertise to refine and scale their product. They partnered with Surfaceink, acquired in 2023 by PwC, which brought comprehensive capabilities in product strategy, design, engineering, and prototyping to the collaboration.
Surfaceink’s extensive background with Internet of Things (IoT) devices and artificial intelligence data integration proved invaluable to the development process. The partnership allowed MakuSafe to leverage advanced technical expertise while maintaining focus on their core mission of improving workplace safety, PwC explained.
Human-Centered Design Approach
MakuSafe understood from the beginning that technical sophistication alone wouldn’t guarantee success—worker adoption was crucial. The development team conducted extensive on-site visits to multiple manufacturing facilities, observing workers in their daily routines to gain authentic insights into real-world use cases and potential pain points, according to the case study.
Worker comfort and safety became paramount design considerations, PwC noted. The team created a detachable armband solution that allows the device to easily break away if accidentally caught on machinery or fixtures—a crucial safety feature in industrial settings. Temperature adaptability was another key innovation, as the team observed widely varying factory conditions; the final design allows comfortable wear over clothing or directly on the arm depending on environmental conditions.
The observations also revealed that personalization would increase adoption rates. Workers were more likely to consistently wear devices that reflected their individuality, prompting designers to offer the wearables in various customizable patterns that allow for personal expression while maintaining functionality, the case study noted.
Technical Implementation
The engineering team developed a sophisticated sensor system that monitors high-decibel sounds, unsafe temperature and humidity levels, low lighting conditions, and are equipped with accelerometers that identify slip or fall events.
Cloud connectivity forms the backbone of the system, enabling real-time data transmission between the wearable devices and a central platform. This connectivity creates a comprehensive monitoring network that provides immediate visibility into workplace conditions and potential hazards as they develop, according to the case study.
The collected data feeds into a custom-designed dashboard that transforms raw information into actionable insights for safety managers.
Impact and Results
The tangible results of MakuSafe’s technology have been substantial. Insurance companies report a 50% decrease in claims submitted by policyholders among MakuSafe’s industrial clients—a significant financial benefit that explains why insurance companies became enthusiastic investors in the technology.
The product development and implementation process has been remarkably smooth, with zero production delays due to engineering issues. This seamless integration into existing workflows demonstrates the thoughtful design process that prioritized worker acceptance and operational efficiency.
“We had a vision for a connected technological solution that could help factories protect and save lives. PwC gave us the design, engineering and strategic support we needed to bring that vision to life,” says Mark Frederick, CTO and co-founder of MakuSafe.
Read the full PwC case study here.